- Home
- Applications
- Caustic Treating
Caustic Treating
The key aspects of a caustic treating system pertain to the degree of contact between the caustic and hydrocarbon to facilitate the mass transfer. Increasing the specific surface area of contact in a two phase system necessarily creates a tight emulsion. The product hydrocarbon often contains entrained caustic, which is not easily recovered by a simple water wash followed by a separator drum. The spent caustic is often regenerated with sour-naphtha stream that is used to extract the disulfide oils into the hydrocarbon phase. The regenerated caustic often carries sour naphtha with it, and the sour naphtha carries caustic with the disulfide oils to the hydrotreater where the caustic will form a crust and reduce reactor life.
- Reduce caustic carryover from the Caustic Treater
- Reduce caustic carryover in the treated hydrocarbon stream
- Reduce caustic carryover in the naphtha used for regeneration
- Reduce hydrocarbon and disulfide oil carryover in the regenerated caustic
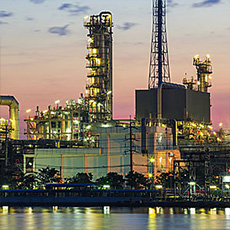
Related technologies
The ProcessOR is a superior separator vessel often used for particle/liquid filtration or separation. It is available to be delivered as a self-contained skid (pictured) or a stand-alone vessel. It is also available custom sized as a capital sale or as a turn-key rental, which is often available within days of the received order.
LiquiSep technology has been implemented specifically to help separate emulsions that are not separable by conventional coalescers. Conventional coalescers are unable to provide the degree clarity associated with LiquiSep technology due to the inability to capture and remove the most penetrating droplets that cause carry-over. LiquiSep can separate these dispersed and emulsified droplets from the hydrocarbon to practically non-detectable levels.
EXTRACTIVE SEPARATIONS - POLAREX
Polarex, US Patent 8425663, an extractive separations technology provides gas processors, chemical manufacturers, and refiners dramatically improved separation of entrained and dissolved contaminants. It is designed to replace conventional water wash and solvent scrubbing towers.
Compared to conventional cartridge filters, COMPAX saves you money by lowering operating costs and reducing disposal costs. When comparing filters with the same efficiencies or Beta ratings, nothing outperforms the cost/performance value achieved with COMPAX.
The Apex element is specifically intended to keep annular velocities constant across the entire height of the element. This is accomplished by introducing a gentle taper in the element, so that the annular space on the outside of the element gradually increased from the bottom to top, keeping pace with the external fluid flow as it exited the element.