- Home
- Technologies
- Compax
The major innovation in COMPAX is its elegant simplicity. It consists of two parts: the COMPAX coreless elements and the reusable core. The reusable COMPAX core is semi-permanently installed into the existing filter vessel without the need for special tools. After installation of the cores, the open end of the COMPAX cartridge slides down over the length of the core and engages a positive sealing O-ring to integrally seal the filter and core together. The reusable cores have standard collapse ratings of 75 or 150 psi, depending on the series and material of construction. Higher collapse ratings are available upon request.
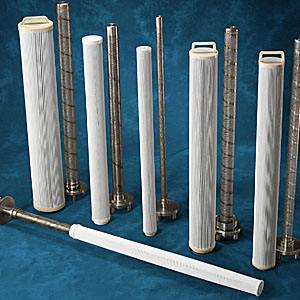
Benefits
- COMPAX saves money by lowering operating costs and reducing disposal costs compared to conventional cartridge filters.
- It offers superior cost/performance value when comparing filters with the same efficiencies or Beta ratings.
- Performance, disposability, and cost-effectiveness make COMPAX the right choice for new filtration applications or upgrading conventional cartridge filter applications.
-
FUNCTIONAL DESCRIPTION
-
COMPAX coreless filters are available with a broad range of media types and micron ratings to match the requirements of the application. The reusable cores have standard collapse ratings of 75 or 150 psi, with higher ratings available upon request. The open end of the COMPAX cartridge slides down over the length of the core and engages a positive sealing O-ring to integrally seal the filter and core together.
-
APPLICATION AREAS
-
If you are currently using a conventional filter – pleated, depth, molded or string wound, nominal or Beta rated – you can have COMPAX performance without purchasing new filters or modifying existing housings. Whether it is for water, amines, chemicals, hydrocarbons, oils, coolants, inks, paints, or other fluids, for prefiltration or final filtration, there is a COMPAX system that is right for the application.
RELATED APPLICATIONS
The key aspects of an alkylation unit pertain to the amount of acid that needs to be made-up on a continuing basis. This cost becomes even more critical if the plant has no onsite acid regeneration, or the acid consumption exceeds the acid regeneration capacity.
BTX (BENZENE, TOLUENE AND XYLENE)
Purify benzene, toluene, and xylene (BTX) from refinery or petrochemical aromatics streams such as catalytic reformate or pyrolysis gasoline. This liquid-liquid extraction processes offers lower capital and operating costs, simplicity of operation, range of feedstock, and solvent performance.
Reactor products can contain gelatinous, deformable solids form in coating formulation. Batch Process: Limited reactor turn-over (constrained through-put) due to long filtration process. Reduce operating costs and batch cycle time, double capacity and increase online life.
Silicones are inert, synthetic compounds with a variety of forms and uses. Typically heat-resistant and rubber-like, they are used in sealants, adhesives, lubricants, medical applications, cookware, and insulation.
Deep Well facilities for the disposal of plant waste streams often employ nominally rated spray spun elements, bags, diatomaceous earth filters, and various other types of conventional filtration technology.
The key to optimizing a hydroprocessing unit is to maximize the life of the catalyst bed and increase energy efficiency of the furnaces.
There are two basic steps to the treatment of natural gas liquids in the natural gas stream. First, the liquids must be extracted from the natural gas. Second, these NGLs must be separated themselves.
Until recently, the Liquefied Natural Gas (LNG) market was a relatively small part of the gas processing world. The market has experienced a transformation fueled by the discovery of vast reserves in North America, Asia’s robust economic growth, larger populations, and the demand for cleaner energy.
There are a number of factors that affect the capacity and operation of a typical amine system. Solid or liquid contaminants in the system may cause foaming. The presence of foaming is typically addressed by the addition of expensive antifoam chemicals and/or by reducing the operating capacity of the amine system.
The key aspects of a caustic treating system pertain to the degree of contact between the caustic and hydrocarbon to facilitate the mass transfer.
Eliminate hydrocarbons in Quench Water system, minimize fouling, provide greater system reliability, lower maintenance, lower energy costs.
Product custody transfer involves a number of processes, all of which are intended to meet transfer specifications in terms of water, particulate and metals.
Proper fluid and proppant placement are critical to a successful propped fracture stimulation treatment.
Many lube oil recovery processes create aqueous and hydrocarbon emulsions that are difficult to separate by means of conventional liquid/liquid separations technology.
Hydrocarbons in the sour water system are typically present on a continuous basis at up to 10,000 ppm and during upsets to levels greater than 50,000 ppm.