- Home
- Technologies
- Intellisep
IntelliSep absorbs contaminants utilizing various filter aids, including clay for jet fuel, Magnesol for bio-diesel, and activated carbon for solvents. The IntelliSep cartridge provides a medium to remove/absorb contaminants and then utilizes filter media to prevent the medium from contaminating the final product, all in a single element. It offers the same results as a filter press and downstream filtration combined in a single vessel, allowing for greater process throughput with less operator burden.
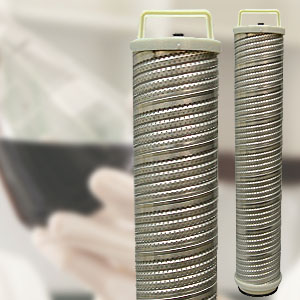
Benefits
- Dependable, robust, and flexible filter aid media cartridge.
- Absorbs contaminants using various filter aids such as clay for jet fuel, Magnesol for bio-diesel, and activated carbon for solvents.
- Enhances chemical processes by reducing operator burden, improving product quality, and minimizing re-processing time.
- Provides the same results as a filter press and downstream filtration combined in a single vessel, allowing for greater process throughput with less operator burden.
-
FUNCTIONAL DESCRIPTION
-
ProcessOR high performance separation vessels are designed with the flexibility to accept IntelliSep cartridges. The vessels create an optimized design for delivering exceptional products while lowering footprint and decreasing capital and operational costs. Additionally, existing vessels can be upgraded by having the design team re-engineer the inside and install IntelliSep cartridges.
Application Areas
Many applications for the IntelliSep have been to replace filter presses on batch chemical processes and continuous chemical processes where traditional treating methods lead to high operator burden, poor quality products, and lost time due to re-processing off-spec products. IntelliSep has been developed to address each of these issues and will enhance the chemical process by providing a filter aid medium in an easy-to-operate envelope.
RELATED APPLICATIONS
Product custody transfer involves a number of processes, all of which are intended to meet transfer specifications in terms of water, particulate and metals.
Natural gas gathering systems deliver large volumes of gas via pipeline to the central inlet of the gas processing facility. Removal of solid contaminants and free liquids present in the inlet gas is critical to the downstream process.
Silicones are inert, synthetic compounds with a variety of forms and uses. Typically heat-resistant and rubber-like, they are used in sealants, adhesives, lubricants, medical applications, cookware, and insulation.
Fuel Gas Streams are frequently contaminated with liquid aerosols. The liquid exists as a stable and persistent “smoke” in the gas stream.
Reactor products can contain gelatinous, deformable solids form in coating formulation. Batch Process: Limited reactor turn-over (constrained through-put) due to long filtration process. Reduce operating costs and batch cycle time, double capacity and increase online life.