- Home
- Applications
- Sour Water
Sour Water
Hydrocarbons in the sour water system are typically present on a continuous basis at up to 10,000 ppm and during upsets to levels greater than 50,000 ppm. As little as 5,000 ppm Cat Naphtha lost to the sour water system from an FCC main fractionator overhead accumulator operating at 100 gpm water represents 262,800 gallons of potential product gasoline lost per year, with a recoverable product value greater than $500,000.
Most sour water systems experience either periodic or continuous hydrocarbon upsets, leading to stripper foaming, diminished capacity, fouling of heat transfer surfaces, and in extreme cases shut down and environmental emissions due to inability to process accumulated sour water.
Adding sour water residence tank capacity to address hydrocarbon carryover to the sour water stripper may require a capital expenditure of several million dollars or more. HRT provides superior hydrocarbon recovery, increased flexibility and a smaller footprint while reducing required capital by over two-thirds. HRT combines both superior performance and superior economic returns.
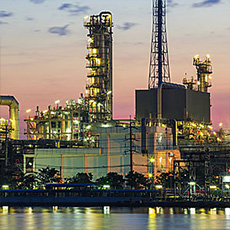
Related technologies
HYDROCARBON RECOVERY TECHNOLOGY - HRT
HRT provides petroleum producers, refiners and gas processors dramatically improved solids control and hydrocarbon recovery from process water streams. Applications for HRT include: Produced Water Management, Oil Removal from Waste Water, and SRU Optimization.
The ProcessOR is a superior separator vessel often used for particle/liquid filtration or separation. It is available to be delivered as a self-contained skid (pictured) or a stand-alone vessel. It is also available custom sized as a capital sale or as a turn-key rental, which is often available within days of the received order.
Compared to conventional cartridge filters, COMPAX saves you money by lowering operating costs and reducing disposal costs. When comparing filters with the same efficiencies or Beta ratings, nothing outperforms the cost/performance value achieved with COMPAX.
LiquiSep technology has been implemented specifically to help separate emulsions that are not separable by conventional coalescers. Conventional coalescers are unable to provide the degree clarity associated with LiquiSep technology due to the inability to capture and remove the most penetrating droplets that cause carry-over. LiquiSep can separate these dispersed and emulsified droplets from the hydrocarbon to practically non-detectable levels.
The Apex element is specifically intended to keep annular velocities constant across the entire height of the element. This is accomplished by introducing a gentle taper in the element, so that the annular space on the outside of the element gradually increased from the bottom to top, keeping pace with the external fluid flow as it exited the element.
V-MAX is a coreless filter that flows from the inside-to-outside like a bag filter but V-MAX technology can offer the same online life as a bag filter in a vessel that is roughly half the diameter. This is possible since the V-MAX design offers up to ten times the available filtration media in the same element envelope.